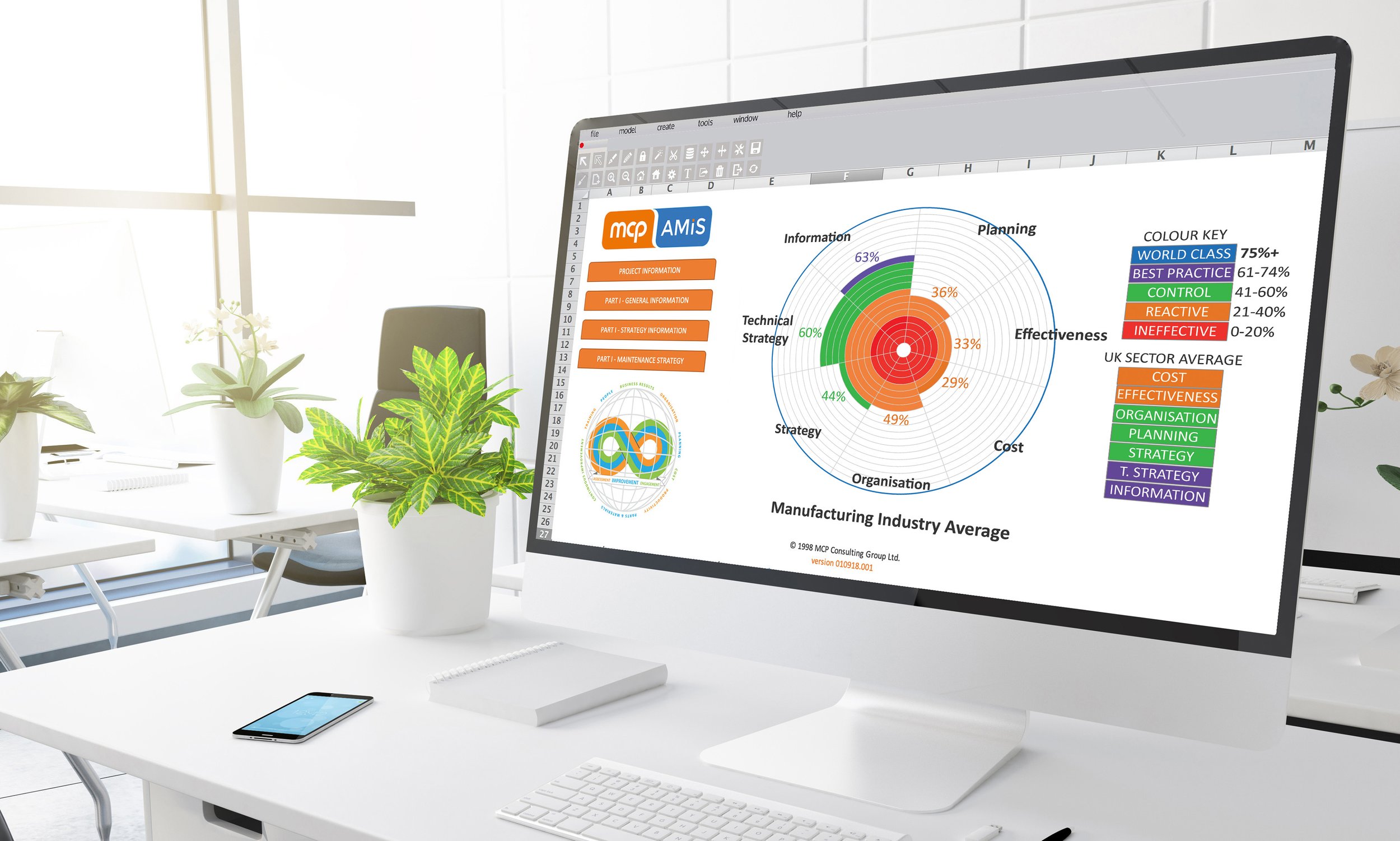
Maintenance Benchmarking
Maintenance Benchmarking with AMIS
For over 30 years MCP has been working with clients all over the world to deliver business improvements in manufacturing and maintenance. Critical to business success is benchmarking, improvement and engagement. A key tool to start your maintenance improvement journey is with AMIS.
To date MCP has conducted their 3-5 day AMIS maintenance benchmarking assessments at over 1,500 sites worldwide and helped in over 6,000 Operational Improvement Programmes in industries ranging from food and drink, chemicals, automotive to pharmaceuticals.
AMIS Maintenance Benchmarking Categories
There are 10 categories that can be harnessed to help in any improvement programme.
Organisation
Is the organisation designed to deliver high performance with clear accountabilities? Is the maintenance workload defined and with the right level of skills? The working relationship between engineering maintenance and operations/production is critical to success.
Work Planning
Planned and unplanned maintenance should be recorded. Maintenance and production management must be involved in new equipment decisions, from the initial concept stage to operation - including planning of future maintenance spares, labour, training and equipment requirements.
Cost Management
Are labour and material cost information available to teams and management to drive improvement? Analysing costs help assess overall equipment effectiveness.
Maintenance
Is your planned preventative maintenance programme effective? Do you know what the real cost of maintenance should be for your plant? Effective plant maintenance is a fundamental requirement to guarantee efficiency and ensure assets are in optimum condition.
Parts and Materials
Does the maintenance team have access to an up-to-date stores catalogue showing all stock items, locations, EOQ, re-order points, including details of consignment stocks and direct supplies? Are the stores lines controlled using a comprehensive computerised inventory management system?
Continuous Improvement
Is there a formal programme that analyses maintenance, technical and cost data and identifies the CI objectives and development of action plans? Are large and repetitive equipment failures formally analysed to determine the root cause of failure and identify any weak components, processes or procedures.
CMMS
The selection and implementation of a suitable system to manage an organisation’s assets can be a daunting task with so many systems available and the preferences of individuals to be considered.
Safety
Does your company have processes in place to operate safely and efficiently? We provide the framework for forward-looking integrated planning, which focuses on incorporating risk-based decisions to deliver objectives effectively and efficiently.
Training
Do the operators and technicians receive technical training on a regular basis? Does the workforce receive approx. ten days of training per year? Have the team leaders received training in team leading and management skills?
People
People are the organisation. Does the organisation encourage an improvement culture? Does the senior management team lead by example? Is there a process for employees to discuss business topics with organisational leaders? Are there processes for measuring and reviewing actual performance against objectives?
AMIS Business Results:
Where companies have wholeheartedly encompassed the AMIS approach and continued on an AMIS Journey,
results have included:
Improved asset management practices
Improved customer satisfaction and service levels
Improved asset performance leading to improved availability and OEE
A consistent and proven approach for World-Class asset management
More cost-effective use of engineering and maintenance resources